Proyecto casero: Rediseño y construcción de la placa electrónica de un coche teledirigido. Desarrollado y escrito por Niva_v_Kopirce.
Llegaron las Navidades y me disponía a regalar a mi sobrino un coche teledirigido chino barato. Siempre me gusta comprobar de antemano si cualquier regalo que contenga componentes electrónicos funciona. Funcionaba bien, sin embargo, al instante me di cuenta de algunas cosas que podrían hacerse mejor y/o actualizarse.
La primera idea fue añadir luces LED en la parte delantera y trasera. Como ya tenía luces de plástico transparente, añadir LED y pegarlas en caliente fue bastante fácil.
La actualización anterior me hizo pensar en la capacidad del pack de baterías original. El pack de baterías original, formado por 6 pilas NiMH, sólo tenía una capacidad de unos 700 mAh. Como seis pilas de NiMH de 1,2 V tienen 7,2 V en total, eso es más o menos lo mismo que dos pilas de ión-litio en serie. Afortunadamente, tenía por ahí un montón de 18650 recuperadas y unas cuantas 16650 con una capacidad de entre 2000 y 2300 mAh. Las 16650 eran casi perfectas.
¿Por qué casi perfecto? Las células de ión-litio completamente cargadas tienen unos 4,2 V, lo que da un total de 8,4 V en serie. Un voltaje más alto significa motores más rápidos, pero como el rotor sólo tiene unas pocas bobinas, actúa como una carga inductiva. Y la conmutación de la carga inductiva provoca picos de tensión: a mayor tensión, mayores picos de tensión. Desafortunadamente, después de algún tiempo, esto llevó a quemar uno de los cuatro transistores de la placa de control del puente en H original.
Aunque sustituí todos los transistores por otros más potentes, añadí los diodos flyback que faltaban y condensadores para reducir los picos de tensión (más adelante explicaré la razón de todo esto), un transistor seguía muriendo. Así que decidí crear una nueva placa de control con transistores MOSFET.
El contenido del artículo se organiza del siguiente modo:
1. ¿Cómo funciona un coche teledirigido?
1.1 Transmisor
El principio reside en el término coche «teledirigido», que sugiere la existencia de un controlador remoto, a menudo llamado transmisor. En términos sencillos, el transmisor convierte la señal humana (aceleración, dirección) en señales eléctricas, que se transmiten por radiofrecuencia (RF) al receptor del coche teledirigido.
Normalmente, el transmisor del coche teledirigido también realiza las siguientes funciones:
- Las señales de entrada humanas suelen estar moduladas o codificadas para que la transmisión no interfiera con las señales de otros controladores.
- Esta señal se divide a menudo en canales, donde cada canal es para una entrada diferente: un canal para la marcha adelante, otro para la marcha atrás, otro canal para la izquierda o la derecha. Un coche teledirigido más avanzado tiene transmisores con aún más canales.
1.2 Estrategia de Control
Según el sistema, hay controles simples y controles avanzados. Los mandos sencillos sólo envían ON/OFF (HIGH/LOW, 1/0) en cada canal, por lo que el coche se mueve a toda velocidad o no se mueve en absoluto. Los sistemas avanzados utilizados en productos comerciales más caros ofrecen una amplia variedad de protocolos de transferencia, cada uno de los cuales funciona de forma diferente.
Por ejemplo, los sistemas avanzados en coches teledirigidos pueden utilizar cualquiera de las siguientes estrategias de control:
- El protocolo analógico denominado modulación por ancho de pulsos (PWM) utiliza un ciclo de trabajo diferente (duración de un pulso ALTO en un periodo) para determinar la velocidad o slew rate; la desventaja puede ser la necesidad de utilizar un canal por señal de entrada.
- Otra opción analógica es la modulación de posición de pulsos (PPM), que combina los pulsos PWM de cada canal uno tras otro en una única señal.
- Los protocolos digitales (serie) serían, por ejemplo, i-BUS o s-Bus, que envían valores digitales.
1.3 Control del Motor
El último paso, después de que el receptor reciba y distribuya las señales en los canales correspondientes, es controlar los motores. Dependiendo de la complejidad, existen motores de corriente continua con escobillas, motores de corriente continua sin escobillas (BLDC) o servomotores:
- El motor de CC con escobillas sólo requiere un controlador sencillo formado por un transistor o, para la opción de accionar el motor en ambas direcciones, el llamado «puente en h».
- El motor BLDC, al ser normalmente un motor trifásico de corriente continua, requiere un regulador electrónico de velocidad (ESC).
- Para la dirección con servomotor, se necesita un controlador de servomotor específico.
Este proyecto tiene por objeto un sencillo coche teledirigido controlado con motores de corriente continua con escobillas, un controlador IC para la dirección y un puente en H para la propulsión.
2. Ingeniería Inversa de la Placa Original del Coche Teledirigido
Obviamente, para conservar la placa controladora original, es necesario conservar también algunos componentes originales del coche teledirigido.
2.1 Lista de Materiales
La placa controladora del coche teledirigido consta de estos componentes:
- Regulador LDO 3V3, paquete SOT-23-3 (LDO significa Low Drop Out) para bajar el voltaje de la batería a 3,3V estables para alimentar el circuito integrado (IC) receptor.
- Receptor IC chino sin marca que funciona a 2,4 GHz, encapsulado SOP-16.
- 12MHz oscilador de cristal para proporcionar la señal de reloj para el receptor IC.
- Controlador de motor MX08E para el motor de dirección, paquete SOP-8.
- 4x transistores BJT (2x NPN, 2x PNP) en disposición de puente en H para el avance/retroceso.
- Otros componentes pasivos, principalmente condensadores para filtrado o resistencias para realimentación.
- Antena.
También había dos transistores en paquete SOT-23-3 cuyo propósito exacto no he averiguado, pero supongo que podrían haber estado allí como puertas AND para controlar las bases de los transistores de puente H.
2.2 Componentes Críticos
Los componentes necesarios para la reutilización del coche teledirigido son el regulador LDO, el circuito integrado receptor, el controlador del motor y condensadores cuyos valores no he podido determinar.
Midiendo y trazando alrededor del circuito original, pude determinar el pinout siguiente para el IC del receptor:
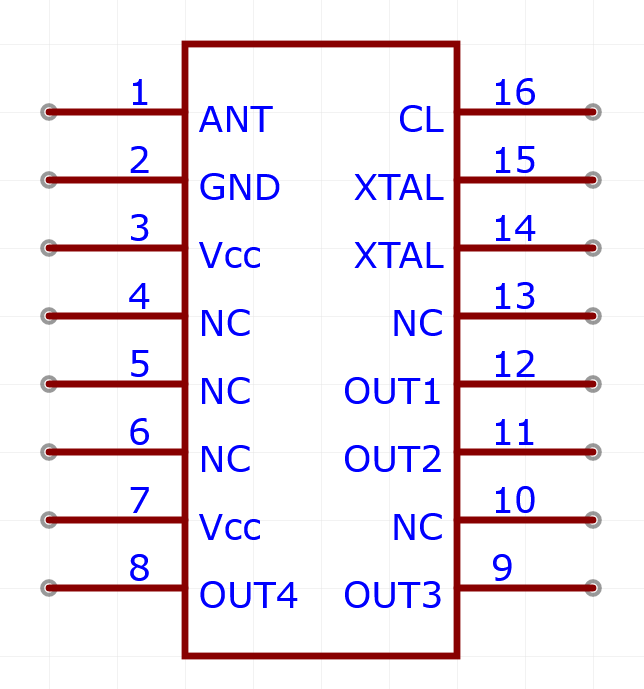
Al pulsar el gatillo para avanzar, OUT1 emite tensión; para retroceder, OUT2 emite tensión; OUT3 y OUT4 son para derecha e izquierda respectivamente.
El controlador del motor de dirección marcado como MX08 era fácil de identificar. Sólo tenía 8 pines: dos entradas, dos salidas, dos pines para masa, una entrada para fuente de alimentación y un último pin no identificado conectado a un divisor de tensión.
Por otro lado, rastrear el regulador LDO fue bastante sencillo.
Eso es todo lo que había que rastrear en la placa original del coche teledirigido.
3. Nuevo Diseño de Placa de Coche Teledirigido
Cuando está claro cómo funciona la placa original del coche teledirigido, es relativamente sencillo diseñar una nueva. Y como se pretende sustituir los transistores originales por MOSFETs, es una buena idea probar si la configuración prevista funcionará. El diseño se dividió en tres partes: pruebas en la protoboard, creación del esquema y fabricación de la nueva placa de circuito impreso.
3.1 Prototipo de Placa de Coche Teledirigido
3.1.1 MOSFETs
3.1.1.1 Fundamentos
Empecemos con algo de teoría. MOSFET es la abreviatura de Metal Oxide Semiconductor Field Effect Transistor (transistor semiconductor de óxido metálico de efecto de campo). Como la mayoría de los transistores BJT, tiene tres terminales, pero aquí se denominan fuente, drenador y puerta. Los MOSFET se utilizan a menudo como interruptores por su velocidad de conmutación.
Su principio de funcionamiento es bastante sencillo. Cerrar un interruptor significa normalmente cerrar el circuito para que pueda circular la corriente. Lo mismo ocurre con el MOSFET: aplicar tensión al terminal de puerta es lo mismo que pulsar un botón. Cuando se aplica una tensión suficiente (por encima del nivel umbral, que se puede encontrar en la hoja de datos normalmente como VGS(th)), la corriente fluye del drenador a la fuente. Sin embargo, esto sólo ocurre con los MOSFET de canal N (N-MOS). Todo es al revés para los de canal P (P-MOS). Cuando la masa está conectada al terminal de puerta, la corriente fluye de la fuente al drenador, por lo que la tensión aplicada al terminal de puerta hace que el P-MOS se cierre.
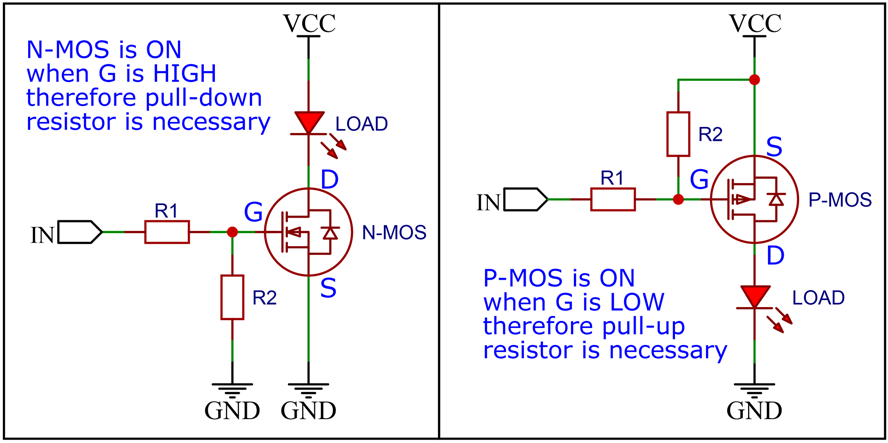
La imagen anterior resume el contenido de esta subsección. Para distinguir el esquema de un MOSFET, el N-MOS tiene una flecha en el lado interior de la puerta y el P-MOS tiene una flecha en el lado exterior.
3.1.1.2 Tensión de Puerta
Mientras que la base del transistor BJT funciona con corriente, la puerta del MOSFET funciona principalmente con tensión. Una cosa importante a tener en cuenta cuando se trabaja con MOSFETs es la puerta flotante. La puerta flotante significa que cuando la puerta no está siendo accionada, capta el ruido ambiente, lo que hace que el MOSFET no funcione correctamente.
Una solución sencilla es añadir una resistencia pull-up/pull-down. Para el N-MOS, se utiliza un pull-down (R2 en la imagen de arriba, izquierda), de modo que cuando la puerta no tiene tensión, debe conectarse a masa, por lo que el transistor permanece cerrado. El P-MOS utiliza un pull-up (R2 en la imagen superior, derecha), conectado a una tensión superior a la tensión umbral.
3.1.1.3 Conmutación Lado Alto/Bajo
El N-MOS tiene la carga conectada a la tensión de alimentación y la fuente a masa; esto se denomina conmutación en el lado bajo porque el interruptor, N-MOS en este caso, está en el lado bajo de la carga.
Por otro lado, el P-MOS utiliza la conmutación en el lado alto. Es la configuración más adecuada, esto se reduce a las reglas básicas de las leyes de Kirchhoff. Dado que la tensión umbral, que determina si el MOSFET se abre o no, viene dada por la diferencia de tensión entre la puerta y la fuente (VGS(th)), poner la carga en el lado bajo significa que la diferencia de tensión entre la puerta y la fuente no puede superar VGS(th).
3.1.1.4 Protección
La resistencia (R1) entre la señal de entrada (IN) y la puerta es una protección. Sabemos que en el mundo real ningún componente es ideal. En este caso la transición entre la puerta y la fuente tiene capacidad de entrada, es decir, actúa como un condensador. Al conectar el condensador a la tensión, la carga instantánea provoca un consumo instantáneo de corriente. Se trata de un breve pico de consumo de corriente hasta que se carga el condensador. Sin embargo, este breve pico de corriente podría dañar el microcontrolador. La resistencia está ahí como protección.
La puerta casi no consume corriente (como ya se ha dicho, ningún componente es ideal), por lo tanto casi no hay caída de tensión a través de esta resistencia y por eso casi no tiene impacto en la conducción de la puerta.
3.1.2 Puente H
3.1.2.1 Fundamentos
El componente ideal del puente en H es el MOSFET. Y el puente en H es el circuito ideal para controlar motores. Conmutar o accionar el motor es relativamente sencillo: basta con un MOSFET para encender el motor o un PWM (también se suele utilizar un MOSFET) para controlar la velocidad. Sin embargo, conducir el motor en sentido contrario es un problema. Los motores de CC necesitan invertir la polaridad para girar en sentido contrario. Esto no es posible con uno o dos MOSFET.
A continuación se muestra la configuración básica del puente en H. Para simplificar, se han utilizado 4 interruptores:
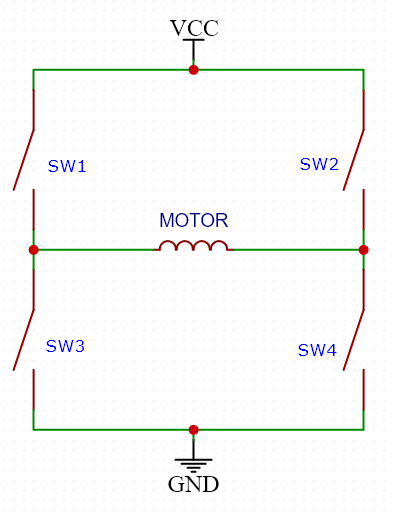
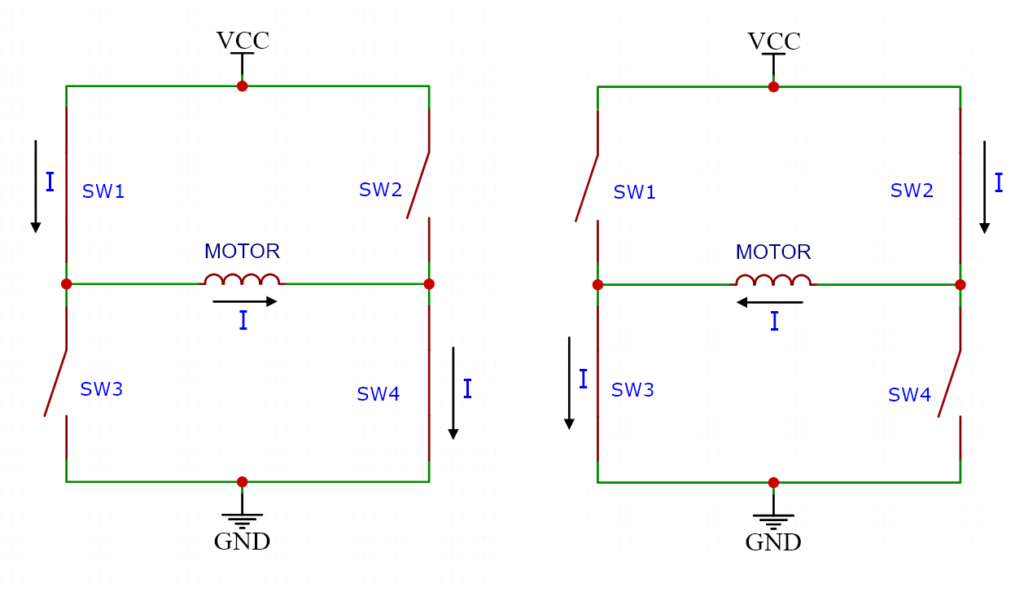
Cerrando SW1 y SW4 se crea un camino para la corriente en una dirección. Si SW2 y SW3 están cerrados, la corriente fluirá en sentido contrario. Es crucial abrir el otro par de interruptores para evitar cortocircuitos. Si SW1 y SW3 estuvieran cerrados al mismo tiempo, la corriente fluiría en esta dirección y como la resistencia allí es muy pequeña, la corriente sería demasiado alta y destruiría los transistores que actúan como interruptores.
En las aplicaciones reales se utilizan MOSFET en lugar de interruptores. A veces se utilizan circuitos integrados completos como puentes en H, pero el principio es el mismo.
3.1.2.2 Protección
Para completar el puente en H, falta una cosa más. Cuando el inductor se desconecta de la fuente de corriente, el campo magnético se colapsa y la energía almacenada debe liberarse en algún lugar. El colapso del campo crea una corriente que fluye en sentido contrario y se denomina flyback. Esto ocurre cuando se invierte el sentido de giro o cuando se suelta el pulsador.
El pico de tensión antes mencionado podría dañar los transistores, por lo que se utilizan diodos para evitarlo. Cada diodo tiene polarización inversa, por lo que los diodos superiores tienen los cátodos conectados a la fuente de tensión y los diodos inferiores tienen los ánodos conectados a masa. La siguiente imagen muestra un puente H completo con diodos flyback. Observe cómo el P-MOS se utiliza como interruptor de lado alto y el N-MOS como interruptor de lado bajo.
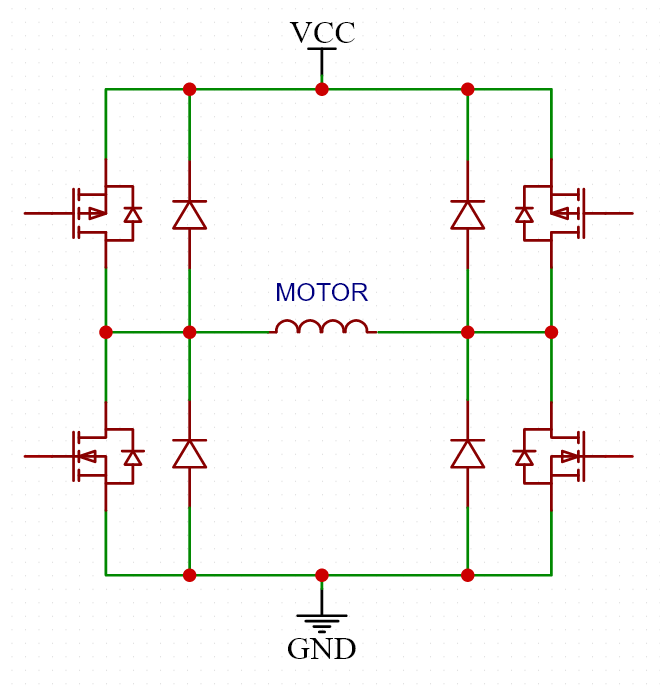
3.1.3 Pruebas en Breadboard
Ha llegado el momento de practicar. Antes de diseñar una nueva PCB (placa de circuito impreso), probar el circuito prototipo es útil para prever posibles problemas. Para probar los prototipos, utilizo protoboards. La protoboard es una placa de plástico perforada que suele constar de 63 filas por 2×5 columnas de agujeros con pinzas de muelle en su interior, conectando siempre una fila a cada lado. Usar breadboard es bueno para proyectos simples como este. No se recomienda usar breadboard para circuitos de alta frecuencia. Las pinzas elásticas de la protoboard tienen características parásitas como alta capacitancia, inductancia e impedancia, por ejemplo, que, al utilizar frecuencias más altas tienen un gran impacto no deseado en el circuito. Para frecuencias más altas, es mejor utilizar una perfboard y soldar directamente a ella. Afortunadamente, esto no es un problema para este puente en H.
3.1.3.1 Conectando el Receptor del Coche Teledirigido
El primer paso fue crear el puente H en la protoboard y probar si funciona correctamente y cambia de polaridad como se desea. Después utilicé el receptor del coche teledirigido, lo soldé a un adaptador de PCB de SOP-16 a 16 DIP (Dual In-Line Package – pines, en mi caso) y probé mi puente en H con el receptor del coche teledirigido original. En la imagen de abajo, aunque no se ve claramente, está la protoboard con el circuito puente H, conectado al osciloscopio.
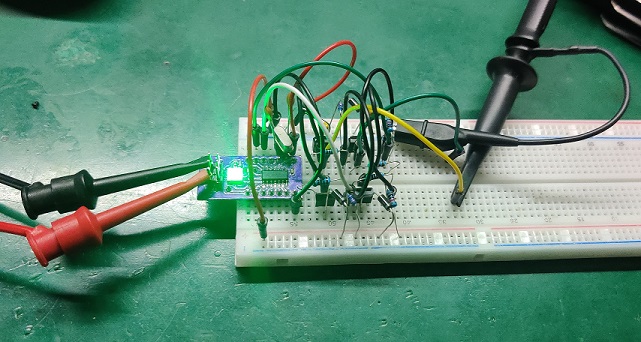
3.1.3.2 Conectando el Motor del Coche Teledirigido
El circuito funcionó como se esperaba, sin embargo, con el motor original conectado, reveló un problema. El problema eran picos de voltaje alrededor de 19V cuando el motor estaba girando. Como se mencionó, los diodos flyback están ahí debido al colapso presentado en las bobinas del motor, pero el rotor giratorio hecho de bobinas, dentro del estator hecho de imanes causa estos picos de voltaje. Una forma sencilla de evitar este problema es añadir condensadores desde los terminales del motor a tierra. En este caso, el condensador funciona como un filtro. La frecuencia de estos picos podría utilizarse para calcular el valor del condensador, pero probé con condensadores de 100 nF y funcionó como esperaba. Por desgracia, no guardé la captura del osciloscopio, así que no hay imágenes.
3.2 Esquemático del PCB del Coche Teledirigido
Cuando el circuito prototipo funciona, llega el momento de diseñar el esquema y, a continuación, fabricar una placa de circuito impreso. Para el diseño esquemático se utilizó la herramienta online de diseño de PCB EasyEDA. Es una buena práctica dividir el esquema en bloques separados para que el esquema sea fácilmente legible y sinóptico.
3.2.1 Puente en H
El puente H final tiene el aspecto que se muestra a continuación.
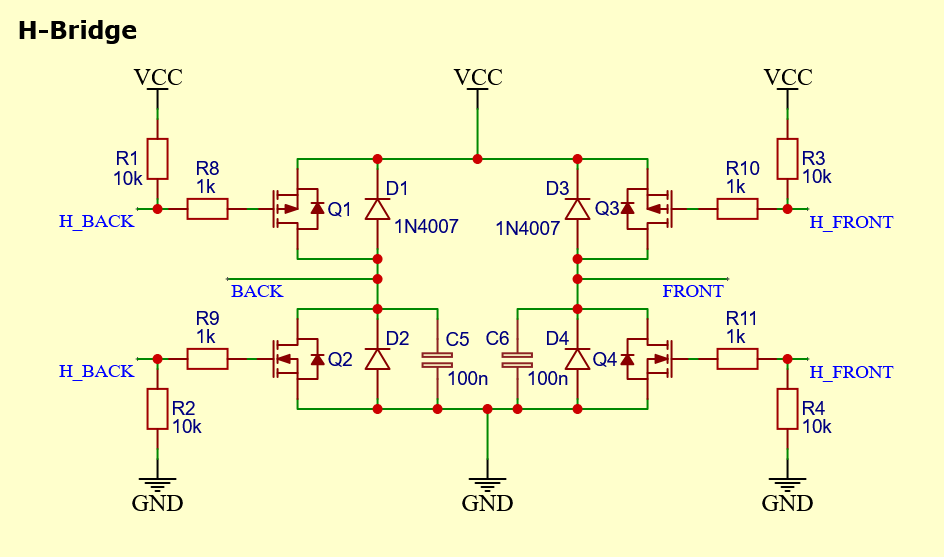
Los cables aparentemente desconectados están en los extremos etiquetados con etiquetas de red (azul). Estas etiquetas de red indican al editor qué cables/trazas debe conectar, aunque no estén conectados físicamente en el editor. Esta función ayuda a organizar mejor el esquema. Funciona igual que los símbolos VCC y GND.
Las etiquetas BACK y FRONT se conectan al conector de salida del motor. H_BACK y H_FRONT se conectan al receptor del coche teledirigido. Cuando se pulsa el pulsador de avance del emisor, la señal H_FRONT está a nivel lógico BAJO (GND) provocando que Q3 P-MOS se abra y manteniendo Q4 N-MOS cerrado. Simultáneamente H_BACK está en nivel lógico ALTO, haciendo que Q1 P-MOS se cierre y Q2 N-MOS se abra, por lo que la corriente fluye en la dirección de las etiquetas/terminales FRONT a BACK. Cuando se pulsa el botón BACK (marcha atrás), la situación es viceversa y la corriente fluye de las etiquetas/terminales BACK a las FRONT.
3.2.2 Circuitos Integrados
Los circuitos integrados se copian de la placa de control original. Su esquema se muestra a continuación.
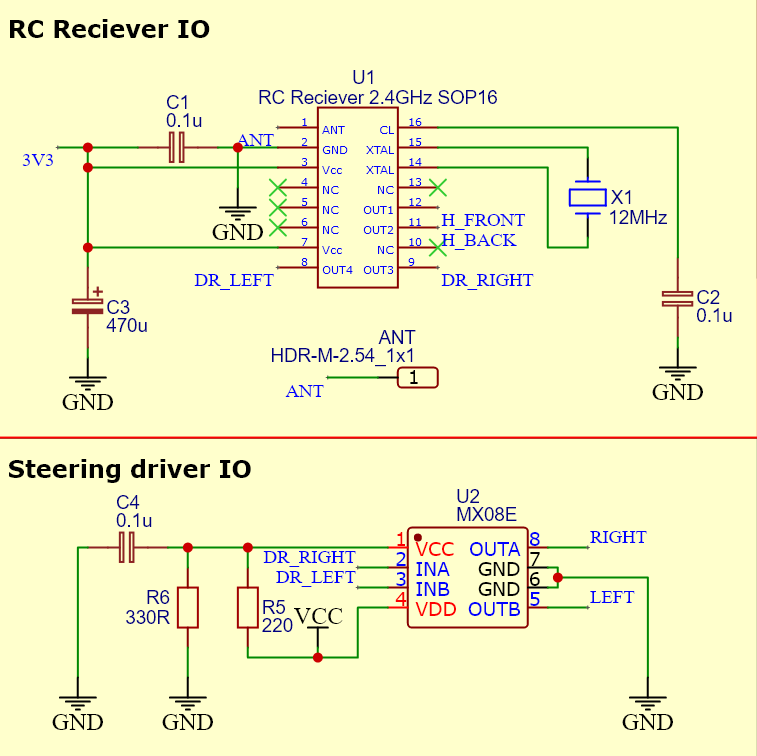
Aquí podemos ver las redes H_FRONT y H_BACK conectadas al receptor U1. Las redes DR_LEFT y DR_RIGHT están conectadas al driver IO U2 para la dirección. Los símbolos verdes «x» en los pines del receptor RC indican al editor que no conecte esos pines. No son necesarios, pero al generar la PCB a partir del esquema no habrá advertencias de que algunos pines no están conectados.
El símbolo U2 fue tomado de la librería de contribución de usuario EasyEDA y en este caso los pines VCC y VDD son engañosos. Para este propósito, es suficiente y decidí utilizarlo de todos modos. Las resistencias R5 y R6 son originales, y como el MX08E no tiene hoja de datos, se desconoce su propósito.
Para la antena usé un pin de cabecera separado, esto crea un agujero en el PCB para soldar la antena.
3.2.3 Resto
Las últimas cosas en el esquema son el regulador 3V3 LDO y los conectores.
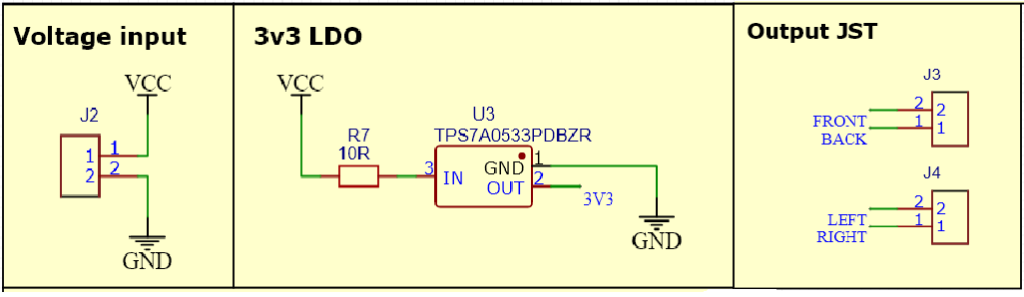
3.3 Diseño del PCB del Coche Teledirigido
3.3.1 Resumen
EasyEDA convierte automáticamente el esquema en la placa de circuito impreso. Con «convierte automáticamente» nos referimos a convertir los símbolos esquemáticos de los componentes en componentes físicos con su correspondiente huella. Las pistas aún no se generan, porque primero hay que colocar cada componente en su lugar.
Hasta ahora los componentes están conectados a través de redes llamadas ratlines. Hay dos formas de rutar (crear trazas físicas a partir de las redes que conectan los componentes): autorutado o manualmente. Autorutado crea trazas automáticamente, pero está limitado por reglas establecidas, no siempre fiables.
Recomiendo rutar manualmente, es un método más fiable. El método manual ocupa la mente, hace pensar en la colocación de cada componente. Por supuesto, lleva unos cuantos intentos hasta que queda perfecto. Normalmente, ruto todo excepto las rejillas de tierra, la razón es que para la tierra utilizo plano de masa. En primer lugar, reduce el ruido generado por altas corrientes y señales de alta frecuencia, en segundo lugar, ahorra tóner y solución de grabado (que se mencionará más adelante).
3.3.2 Posicionamiento Automático
La siguiente imagen muestra los componentes posicionados automáticamente por EasyEDA y conectados por líneas azules.
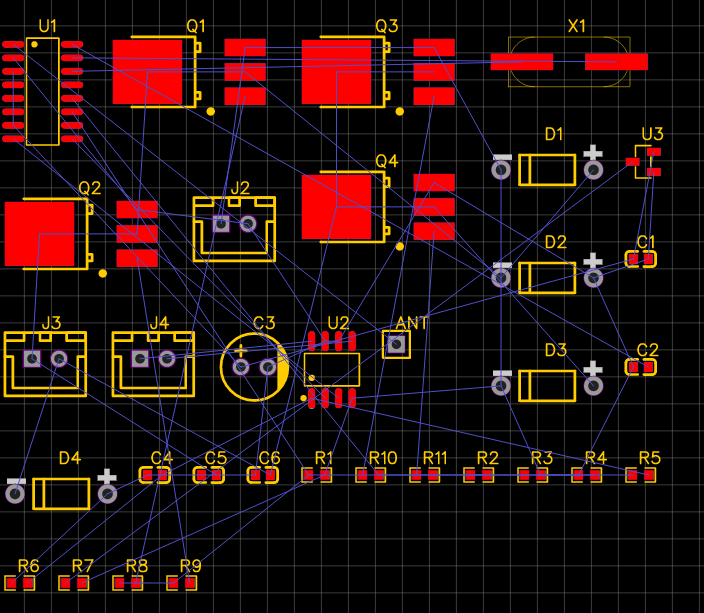
Los rectángulos rojos corresponden a la capa superior de cobre de una placa de circuito impreso, mientras que las líneas amarillas son los contornos de los componentes. Si hay piezas colocadas en la capa inferior, el color sería azul para las trazas de cobre y verde para los contornos de los componentes. Además, los círculos grises son los pads de las capas superior e inferior, llamadas multicapa.
Es importante mantener los componentes con más de tres terminales en la misma capa que el resto del componente, ya que de lo contrario se reflejaría la traza.
EasyEDA también genera el contorno de la placa que es de color púrpura, yo suelo quitar el contorno de la placa ya que no es necesario.
3.3.3 Restricciones PCB Casera
Cuando se construye una placa de circuito impreso casera, hay que tener en cuenta la placa física que se va a grabar. Los factores principales son el número de capas y el tamaño. La placa de control será de una sola cara. En cuanto al tamaño, tengo una placa FR4 (epoxi de 0,6 mm) de 10×10 cm que cortaré al tamaño deseado.
Para el diseño del tamaño de la placa de circuito impreso siempre intento diseñar la placa más pequeña posible teniendo en cuenta todos los factores necesarios, como la disipación del calor, por ejemplo.
3.3.4 Localización y Rutado
Los conectores y todos los componentes THT (tecnología de agujeros pasantes) se colocan en la capa inferior sin cobre. Todos los componentes SMD (dispositivo de montaje en superficie) se dejan en la capa superior.
En la práctica, la capa sin cobre mira hacia arriba, ergo debería llamarse capa superior, y el lado con componentes SMD mira hacia abajo, ergo debería llamarse capa inferior. Sin embargo EasyEDA por defecto utiliza el rojo como la capa superior y porque tengo la mayoría de los componentes SMD, me refiero a la capa de cobre con SMDs como la capa superior.
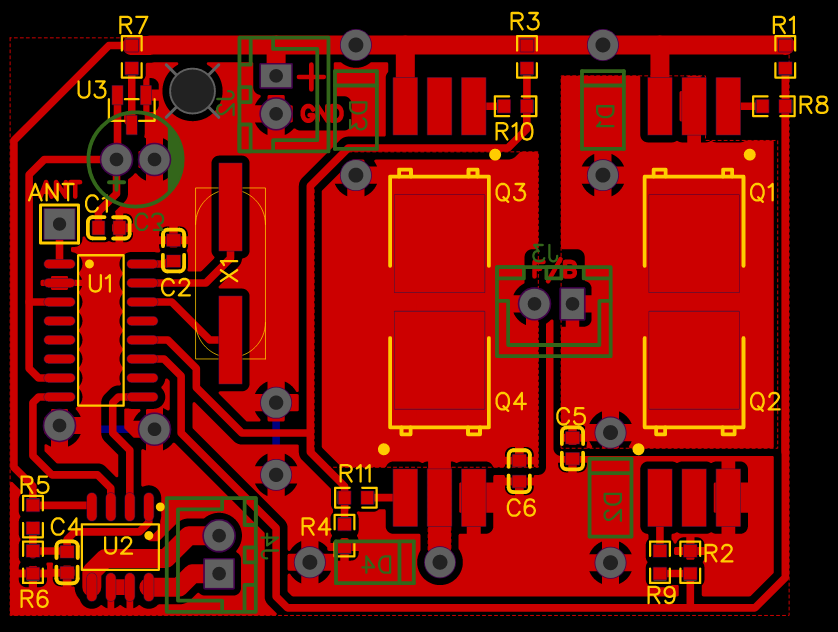
La imagen de arriba muestra el diseño final de la placa de circuito impreso.
- Los MOSFETS se colocaron en pads de cobre comunes, para que disipen el máximo calor posible, pero también ocupen el mínimo espacio.
- La colocación de condensadores de desacoplamiento (C1 y C4) más cerca de los pines de entrada de tensión es vital, de lo contrario pierden su propósito.
- También fueron necesarios dos puentes para conectar los planos de masa (2 pads multicapa debajo de U1 y dos perpendiculares más a la derecha, conectadas por la traza azul).
- Para señales con corrientes más altas, se necesitan trazas más anchas. La anchura de la traza puede calcularse en línea.
3.3.5 PCB Casero
La PCB mejorada para el coche teledirigido se fabricó y pobló siguiendo el procedimiento descrito en el anexo al final de este artículo. Las siguientes imágenes muestran los resultados obtenidos.
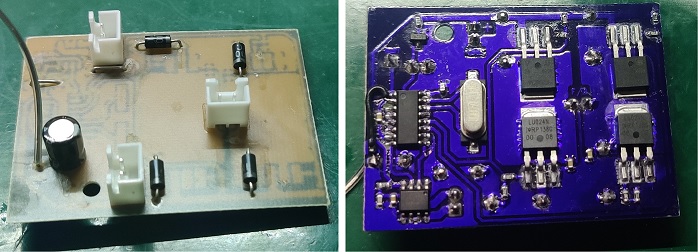
4. Coche Teledirigido Mejorado
4.1 Sondaje, Pruebas y Montaje
Antes de colocar la placa de control en el coche teledirigido, hay un último paso y es probar la funcionalidad de la placa.
En primer lugar, inspeccione si no hay errores en la colocación de los componentes y, a continuación, la funcionalidad eléctrica. Midiendo la resistencia del conector de tensión de entrada, podemos asegurarnos de que no hay cortocircuito o una resistencia demasiado baja.
Si la resistencia es razonablemente alta, el siguiente paso es conectar la placa de control a la fuente de alimentación del banco y comprobar el consumo de corriente, que no debe ser demasiado alto ni nulo.
Cuando la corriente es correcta, el siguiente paso sería medir la tensión de salida correcta del regulador LDO. Si el regulador LDO produce la tensión deseada y la tensión de entrada del CI del receptor de coche teledirigido es correcta, es el momento de probar la funcionalidad nominal.
Conecte ahora los conectores de salida de los motores al osciloscopio. Al pulsar el botón de avance o retroceso del mando a distancia, deben producirse los cambios de señal correspondientes. La placa de control en funcionamiento se coloca en el coche teledirigido y se prueba. Cuando todo funciona como se espera, se monta el coche teledirigido.

4.2 Resultados
Por último, este vídeo muestra cómo funciona el coche teledirigido:
A. Anexo: Fabricación Casera del PCB del Coche Teledirigido
Una vez terminado el diseño de la placa de circuito impreso, llega el momento de crearla. Yo utilizo película seca fotosensible para fabricar las placas de circuito impreso (otro método, por ejemplo, es la transferencia por calor planchando el tóner impreso en un fotopapel sobre el cobre). Para este método se necesitan las siguientes herramientas/dispositivos:
- Impresora láser (cuanto mayor sea la resolución, mejor)
- Hoja transparente para impresora láser
- Algún programa para editar PDFs (se utiliza Photoshop, también se puede utilizar GIMP)
- Película fotosensible (negativo)
- Luz UV (395 – 405 nm, prefiero los LED UV)
- Dos láminas de vidrio
- Plastificadora (normalmente el formato A5 es suficiente, pero el A4 está más disponible)
- Solución de grabado (cloruro férrico Fe2Cl o persulfato sódico Na2S2O8)
- Solución reveladora negativa (carbonato sódico Na2CO3, también conocido como ceniza de sosa)
- Productos químicos de limpieza (acetona, hidróxido de sodio NaOH)
- Papel de lija
- Recipientes de plástico para productos químicos
Otras herramientas son opcionales para soldar SMD:
- Placa térmica PTC
- Pasta de soldar
- Lata de aluminio
La creación del PCB se divide en 8 fases:
- Impresión de una máscara de diseño
- Preparación de la capa de cobre del PCB
- Transferencia de la máscara al cobre
- Revelado de la máscara
- Grabado y limpieza de PCB
- Crear una capa de protección
- Creación de plantillas
- Poblar el PCB
A.1 Impresión Máscara de Diseño
A.1.1 Exportar Archivos
El diseño de la placa de circuito impreso se exporta en formato PDF o SVG. El diseño debe exportarse como negativo, blanco sobre negro y reflejado. En EasyEDA esto se hace en el siguiente menú: Archivo > Exportar > PDF (SVG). En la ventana de exportación seleccione Blanco sobre negro, TopLayer, MultiLayer y Agujero, todo reflejado y haga clic en Exportar.
A continuación se exporta también TopSolderMaskLayer, negro sobre blanco, sin reflejar, que se utilizará para la capa de protección y finalmente se editará para la máscara de esparcido.
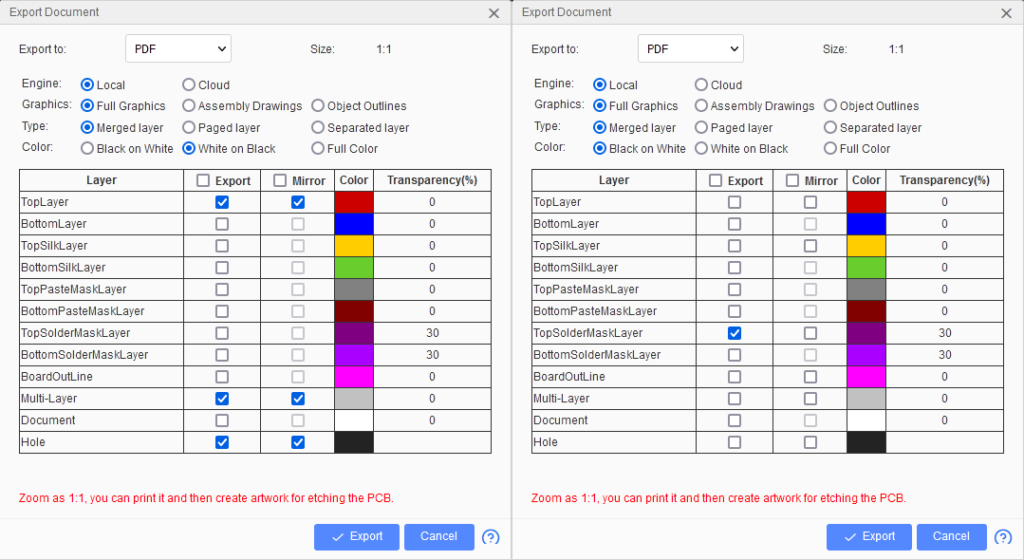
A.1.2 Editar Archivos
Los archivos exportados se editan en Photoshop con la mayor resolución posible (cuidado, los archivos temporales ocupan mucho espacio en disco, yo uso 4200 DPI). La resolución se nota en la hoja transparente.
La impresión en la hoja transparente requiere dos capas de la máscara de negativo, de lo contrario la luz UV pasará a través de una sola capa. (Es posible imprimir sobre papel de calco, por desgracia, no he conseguido buenos resultados, aunque no le he dedicado demasiado tiempo). Se colocan dos copias del negativo del esquema de la placa de circuito impreso, una al lado de la otra.
Por último, la capa de máscara de soldadura se duplica en el archivo de photoshop del diseño de la PCB y también se hacen dos copias. El stencil opcional también utiliza máscara de soldadura, sin embargo hay que eliminar algunos pads innecesarios, yo mantengo sólo aquellos pads a los que necesito aplicar pasta de soldadura (componentes SMD).
A continuación se muestra la edición definitiva:
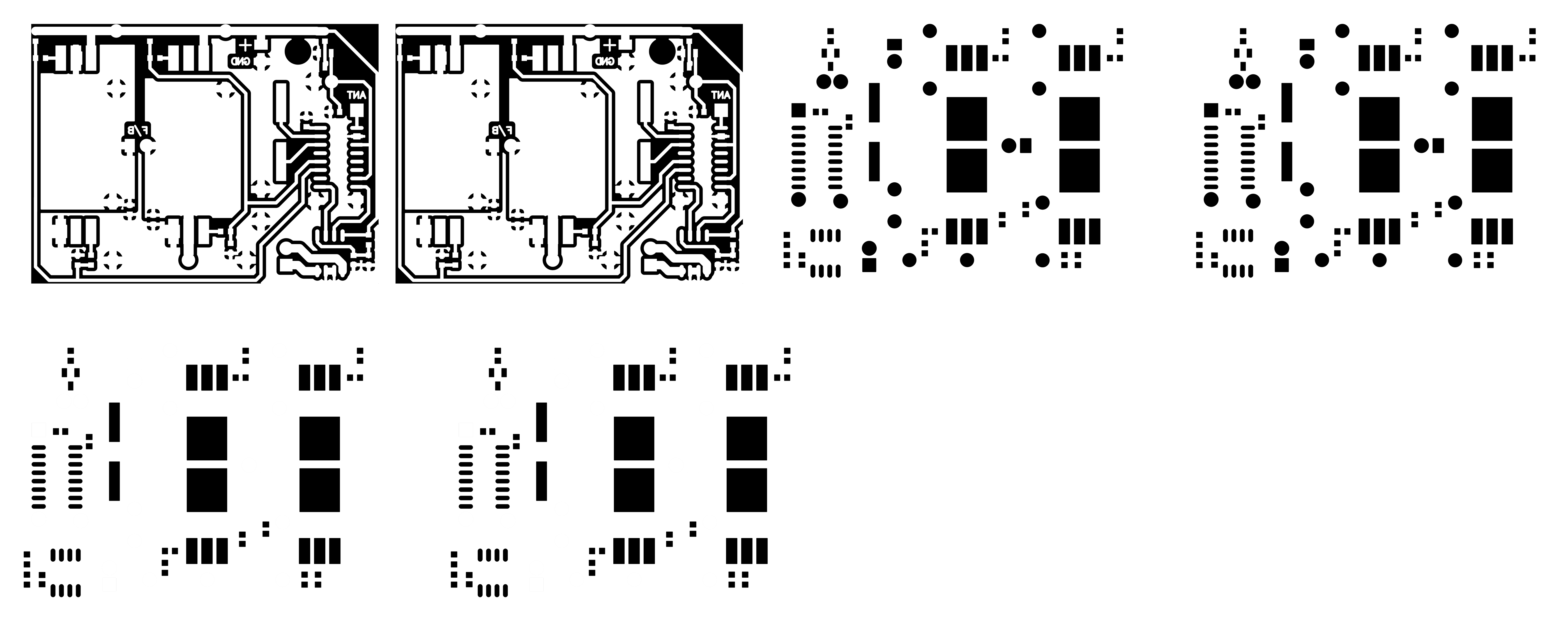
A.1.3 Resultados
El hecho de que se utilice película negativa fotosensible en seco hace necesario el uso de negativos para el diseño de circuitos impresos. La regla es que lo que se expone a la luz UV se pega al cobre, y lo que se pega al cobre no se graba. Por lo tanto, las trazas y los pads deben ser blancas en el diseño, para que no se graben. Cuando se utiliza con planos de tierra también ahorra una gran cantidad de tóner y menos cobre grabado significa más uso de una solución de grabado. Lo mismo ocurre con la capa de protección y el stencil, lo único que hay que enmascarar son los pads.
Tras la impresión, cada par de bloques se coloca uno encima del otro y se unen con cinta adhesiva para formar una máscara perfecta. La capa de tóner impresa debe quedar hacia abajo.
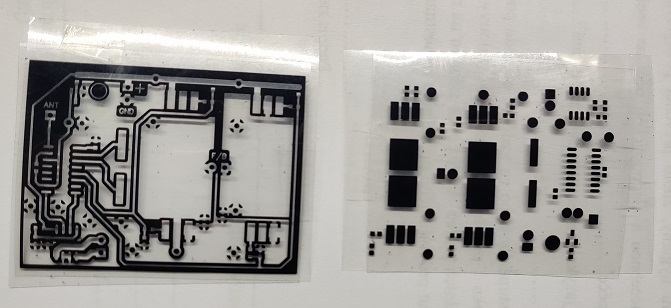
A.2 Preparación de la capa de cobre del PCB
Primero se calienta la laminadora, lo que ahorra tiempo. Para que la película fotosensible seca se adhiera bien al cobre, primero hay que limpiarlo. Una buena opción es utilizar papel de lija al agua, de grano en torno a 800-1000, y luego lijarlo bajo agua caliente, sobre todo alrededor de los bordes; a continuación, límpialo con acetón y papel de cocina para eliminar cualquier resto de grasa y sécalo. A continuación, seque el cobre con cuidado, evitando tocarlo con los dedos.
La película fotosensible seca tiene tres capas. La película mate superior, la película fotosensible intermedia y la película protectora brillante inferior. Para pegar la película al cobre, se retira la película mate. Se aplica presión desde el centro de la placa de circuito impreso hacia los bordes para evitar la formación de burbujas.
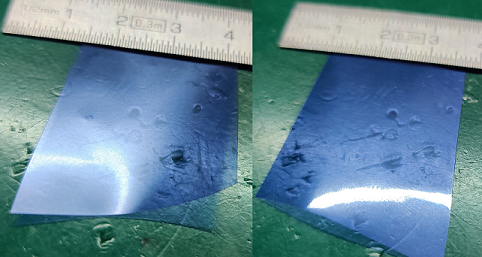
Cuando se calienta el laminador, la placa de circuito impreso con la película se coloca entre el papel doblado, esto es para evitar que la capa fotosensible se pegue a los cilindros de calentamiento (no me preguntes cómo lo sé). El calor de la laminadora y la presión hacen que la película se contraiga y se pegue al cobre. Por último, con cinta adhesiva, se coloca la máscara de PCB impresa sobre la película, con la cara brillante hacia arriba, para que el texto sea legible (no se refleje).
También es aconsejable exponer la película seca a la menor cantidad de luz posible antes de curarla con luz UV.
A.3 Transferencia de la Máscara al Cobre (curado UV)
Para el curado UV se utilizan 4 leds UV de 3 W (400-405 nm, ángulo de cono de 140°). Están a una distancia de 10 cm de la placa curada y de 10 cm entre sí.
La placa de circuito impreso se coloca entre dos láminas de cristal, de modo que el negativo impreso quede presionado lo más cerca posible de la película fotosensible seca.
El curado tarda entre 2 minutos y 45 segundos y 3 minutos. El tiempo de curado depende de la potencia y la distancia de la luz UV utilizada; además, si se utiliza papel de calco, puede llevar más tiempo transferir la máscara correctamente. El paso crucial tras el curado es dejar que la polimerización haga su trabajo y dejar reposar la PCB curada durante al menos 15 minutos, con la cara curada hacia abajo para protegerla de cualquier luz UV adicional no deseada. Tras la polimerización adicional, el contraste debería ser mayor y la película curada se adherirá mejor.
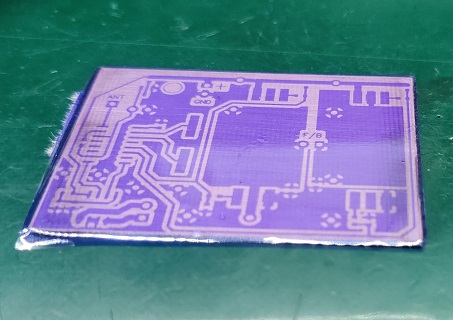
Utilice siempre gafas de protección UV cuando trabaje con luz UV.
A.4 Revelado de la Máscara
Durante el reposo de la polimerización, se prepara la solución de revelado negativo. Yo utilizo carbonato sódico (Na2CO3), conocido como ceniza de sosa, en una proporción de 1:10 con agua destilada. Para 200 ml de agua destilada, se utilizan 20 g de Na2CO3. Para el almacenamiento a largo plazo, es conveniente utilizar un recipiente de plástico sellado. La concentración disminuye con el uso, pero hasta ahora mi primer lote ha desarrollado decenas de PCB en medio año.
Para revelar la capa fotosensible, hay que despegar con cuidado la capa protectora brillante. La placa de circuito impreso no se sumerge en la solución, sino que se cepilla con un pincel empapado en solución reveladora. La película no curada reaccionará con la solución reveladora, creando una capa blanquecina; tras unos minutos de cepillado, la capa fotosensible desaparece. Una vez revelada la película, es necesario lavar los restos con agua, preferiblemente con un cepillo de dientes suave. Si alguna traza está dañada (como la de la parte inferior central de la placa de circuito impreso), puede fijarse con rotulador permanente resistente al agua de 0,3 mm.
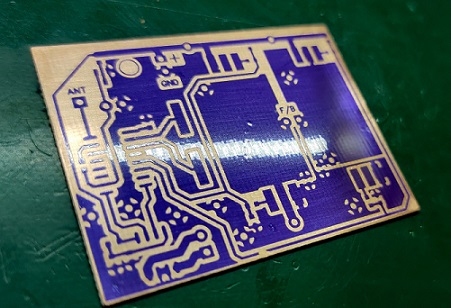
A.5 Grabado y Limpieza del PCB
Existen varios métodos para grabar una placa de circuito impreso de cobre. O bien utilizando cloruro férrico, que puede ser un desastre si no se utiliza con cuidado, o ácido clorhídrico mezclado con peróxido de hidrógeno acelerado con electrólisis (sin embargo, el ácido clorhídrico es altamente corrosivo y cáustico), o utilizando persulfato de sodio calentado, que parece ser el método más limpio y seguro. No obstante, utilice siempre guantes de nitrilo y protección ocular cuando manipule productos químicos.
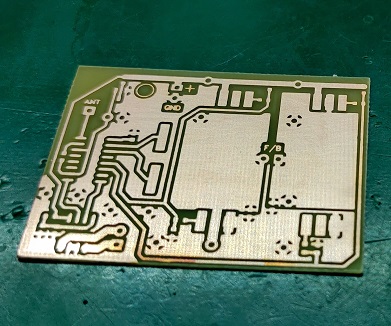
Para preparar la solución de grabado con persulfato sódico, mezcle 20 g de persulfato por 100 ml de agua. Para conseguir un tiempo de grabado razonable es necesario calentar la solución a 40-50°C. El proceso de grabado dura entre 5 y 10 minutos, aunque una solución más fuerte puede acelerar el tiempo de grabado. El grabado se realiza cuando no hay manchas de cobre expuestas. Tras el grabado, debe retirarse la película fotosensible. Para ello, sumerja la placa grabada en una solución de hidróxido de sodio (NaOH) durante unos minutos y luego enjuáguela con agua del grifo. Ahora es un buen momento para taladrar agujeros si es necesario. La placa grabada se muestra en la imagen superior. La ligera oxidación se debe a haber dejado la PCB demasiado tiempo en la solución de hidróxido de sodio, esto se puede eliminar lijando un poco la placa.
Antes de colocar la película protectora opcional o los componentes en la PCB grabada, es una buena práctica sondear las trazas para asegurarse de que no hay cortocircuitos entre ellas ni interrupciones. Si todo está bien, continuemos.
A.6 Crear una Capa de Protección
Este paso es opcional, pero protege las trazas de cobre de la oxidación. Otra opción sería utilizar estaño líquido y sumergir la PCB en el estaño líquido durante unos segundos, la capa de estaño no suele oxidarse. Sin embargo, una desventaja del PCB estañado es cuando se utilizan componentes SMD, además el precio del estaño líquido no merece la pena. La película protectora ayuda a evitar puentes al soldar componentes con pasta de soldadura y placa térmica.
La película seca fotosensible no suele soportar un calor demasiado elevado, pero es una solución diy razonable. En la industria, se suele utilizar una pasta sensible a los rayos UV que se extiende sobre la placa de circuito impreso y luego se expone a la luz ultravioleta durante unos minutos. En un entorno de aficionado, este método es engorroso y no produce resultados satisfactorios debido a la distribución desigual de la pasta, pero por otro lado es más duradero y puede soportar más calor que la película seca. Hay algunas otras opciones también, pero me centro en este método diy barato de usar película seca.
El proceso para hacer la capa de protección es el mismo que para grabar la PCB, así que seré breve. El primer paso es limpiar la PCB con papel de lija y aceton. El segundo paso es pegar la lámina seca a la PCB. A continuación, después de dejar que la PCB pase por el laminador, se coloca la máscara de soldadura impresa encima y se expone a los rayos UV. Después de dejar que la polimerización haga lo suyo, se retira la película protectora y, por último, se revela en carbonato sódico. La exposición adicional a los rayos UV hará que la película sea más duradera.
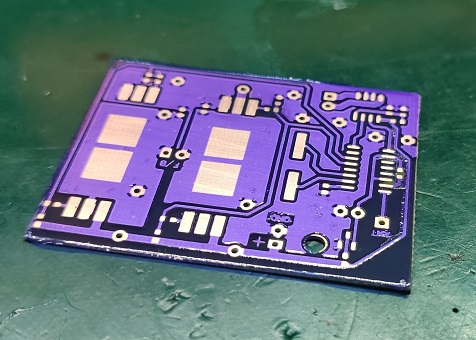
A.7 Hacer una Plantilla (Stencil)
A.7.1 Placa Stencil
En este punto, la PCB está lista para ser rellenada con componentes. Pero soldar componentes SMD con un soldador normal puede ser un reto para los principiantes y requiere cierta habilidad.
Lo más cómodo es utilizar pasta de soldar y dejar que la placa térmica haga el trabajo. Pero la pasta de soldadura es molesta para trabajar sin el uso de dispensador, e incluso entonces, puede ser una pesadilla, cuando la pasta de soldadura no se queda en los pads de cobre sino en todas partes.
En la industria se utiliza una placa de estarcido, que es una fina lámina de acero (de 0,05 mm a 0,3 mm) con orificios grabados. Sobre esta lámina de acero se extiende la pasta de soldadura, lo que da como resultado la cantidad deseada de pasta de soldadura en los pads de cobre.
En un entorno de hobby podemos utilizar casi la misma técnica aunque en lugar de utilizar acero podemos utilizar una lata de aluminio, de una lata de cerveza por ejemplo. Cortando la parte superior e inferior y cortando el resto por la mitad obtenemos una cantidad bastante útil de papel de aluminio para la plantilla. El interior de la lata está recubierto con una película de epoxi y el exterior tiene pintura, ambos deben ser eliminados. Para quitar la pintura y el epoxi, la acetona sólo es eficaz después de precalentar el papel de aluminio.
A.7.2 Procedimiento
La creación de la plantilla para la pasta de soldadura utiliza el mismo método que para la creación de la placa de circuito impreso, salvo que en lugar de utilizar persulfato sódico para el grabado, se debe utilizar cloruro férrico calentado. Para la máscara se utiliza la capa de máscara de pasta de EasyEDA exportada.
El resto del planteamiento es el mencionado anteriormente, es decir, limpiar la lámina de aluminio con acetona, pegar la lámina seca sobre la lámina, utilizar la laminadora para una mejor adhesión, cubrir las máscaras impresas con lámina transparente, exponer a UV, polimerizar, revelar y grabar. Para el grabado es conveniente cubrir una cara con cinta adhesiva, u opcionalmente dejar la capa de epoxi sobre la lámina y retirarla más tarde.
La imagen siguiente muestra la plantilla obtenida.
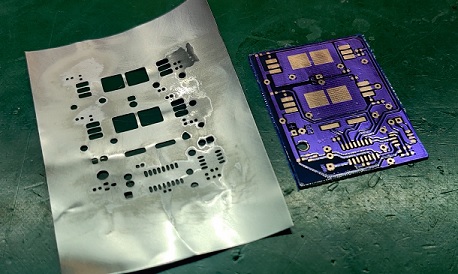
A.7.3 Extender la pasta de soldadura
Para extender la pasta de soldadura sobre la plantilla, la placa de circuito impreso debe fijarse junto con la plantilla. En la imagen de abajo puedes ver el hueco entre la PCB y la plantilla causado por los bordes de la plantilla que se pegan al escritorio haciendo que se curve hacia arriba. No es un gran problema, sin embargo, un método más conveniente es utilizar algunas PCB sin usar (del mismo grosor), ponerlas alrededor de la PCB grabada y pegarlas con cinta adhesiva.
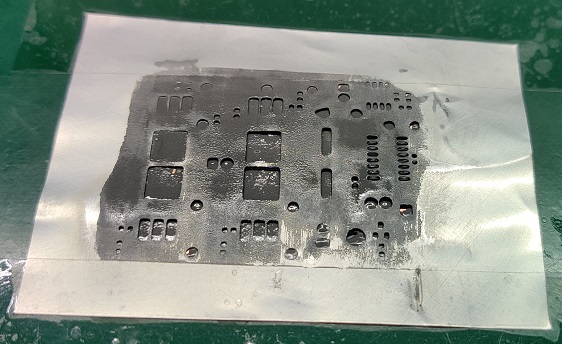
Y la regla general es que cuanta menos pasta de soldar, mejor. Cuando se aplica demasiada pasta de soldar, los componentes pequeños, como las resistencias, tienden a levantarse, o la pasta de soldar forma grandes gotas, lo que dificulta que los componentes permanezcan en el mismo sitio o se alineen con los pads. Para extender la pasta de soldar se puede utilizar una tarjeta de crédito vieja, una escobilla de goma o cualquier objeto plano y duro.
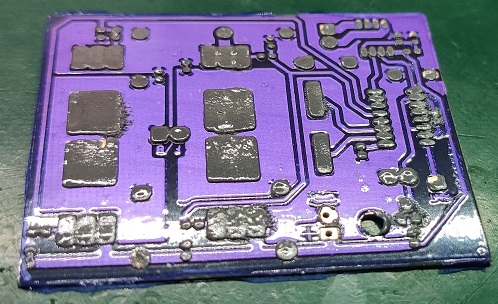
Tras retirar con cuidado la plantilla y limpiar la placa de circuito impreso con isopropilalkohol, se pueden introducir los componentes en la placa.
A.8 Poblar el PCB
Se recomienda poblar la PCB (con pasta de soldadura aplicada) lo antes posible. Empezando siempre por los componentes más pequeños, porque cuando ya están los grandes es muy incómodo manipular con los pequeños.
Una vez poblada, es el momento de precalentar la placa de cocción y el reflujo, que consiste en fundir la pasta de soldadura en la soldadura. Al comprar pasta de soldadura de una fuente confiable, siempre debe incluirse la curva o perfil de reflujo recomendado y seguirlo produce el mejor resultado.
Si compras pasta de soldar barata de aliexpress o una fuente similar, funcionará en cualquier caso, pero colocando la PCB grabada y poblada en la placa de calor antes de que alcance su temperatura máxima, te aseguras de evitar cualquier choque térmico. Lo mismo ocurre con el enfriamiento del reflujo terminado, para evitar cualquier choque térmico enfriar el PCB debe hacerse lentamente.
A continuación se muestra la PCB poblada antes del reflujo y la PCB casi terminada después del reflujo. Durante el reflujo, la película protectora seca se oscurece y se vuelve más adhesiva pero quebradiza debido a la alta temperatura. Después de rellenar la otra cara de la PCB, la placa de control del coche teledirigido está terminada.
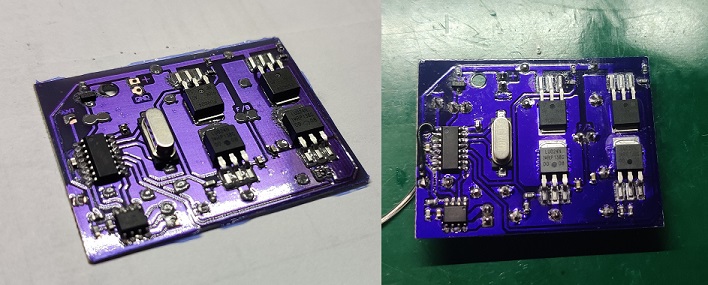
Suscripción
Si le ha gustado esta contribución, no dude en suscribirse a nuestro boletín: